
In the modern textile industry, high quality fabrics have become the mainstream pursuit of the market. As one of the core raw materials in this field, nylon high elastic yarn has gradually emerged with its excellent performance. Today we will learn more about the difference between the two specifications of nylon high elastic yarn 70D and 140D and their respective application scenarios.
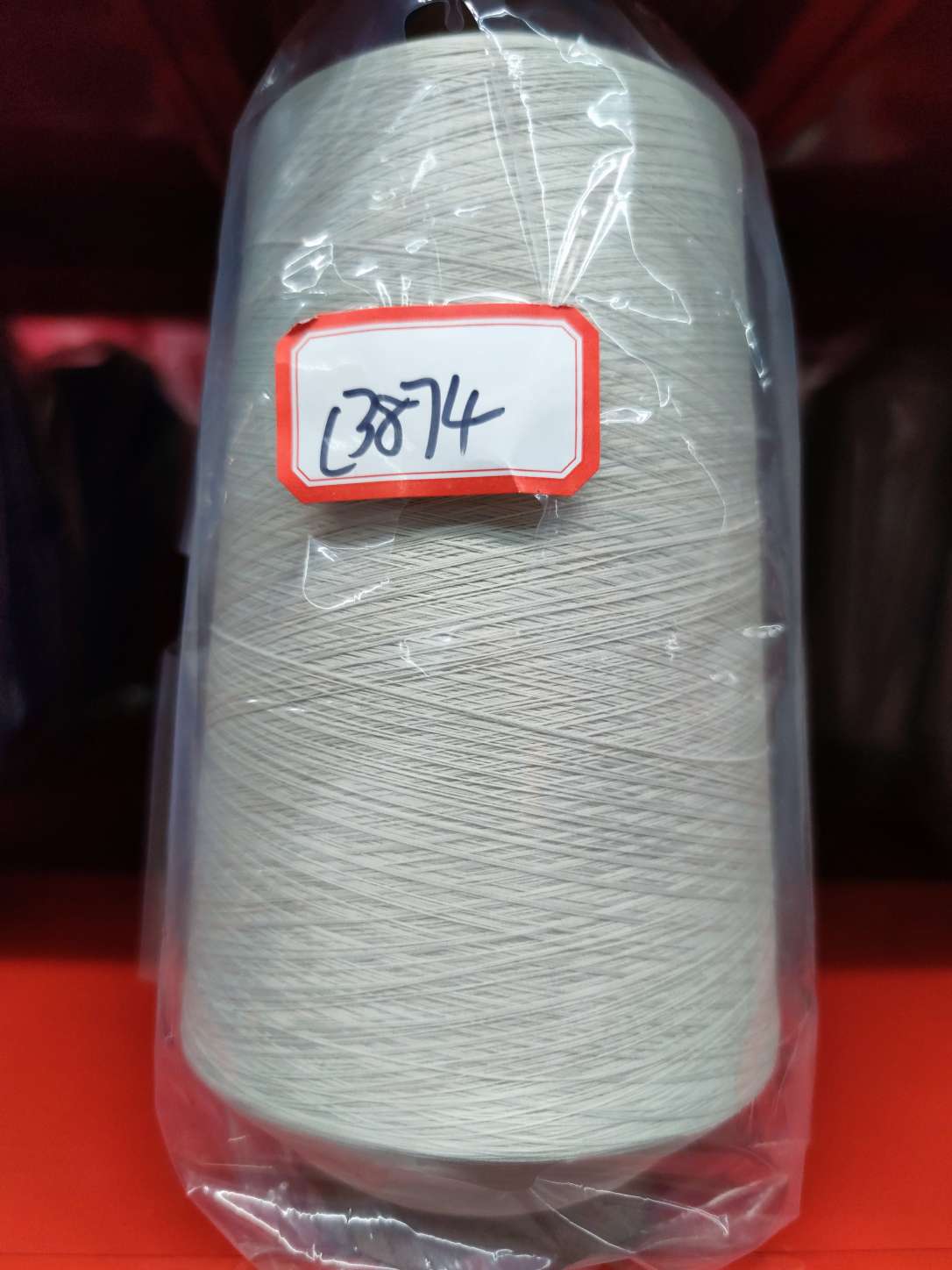
First of all, from the basic characteristics, nylon high elastic yarn 70D is famous for its light, thin and soft characteristics, especially suitable for making sportswear, underwear and other products that have higher requirements for breathability and close-fitting feeling. In contrast, the 140D is more heavy and strong, and is often used for outdoor equipment or protective clothing, such as hiking pants and windproof jackets.
In addition to the different densities, the two have one thing in common is the use of spandex coating process. This technology gives the fabric excellent extensibility while retaining good recovery ability, so that the wearer can feel an unprecedented comfort experience whether it is during strenuous activities or long periods of sitting.
But do you know how such a magical effect is achieved? The answer lies in the rigorous and meticulous production process. Every step from the selection of raw materials until the final packaging and warehousing needs to be carefully controlled and quality standards are not slackened. First, the raw silk is pretreated to remove impurities, then mixed in proportion to form composite fiber bundles, then twisted and fixed in shape by precision machines, and then set at high temperature to ensure that all indexes reach the expected level. Finally, it enters the inspection and packaging process and is ready to be delivered to customers for use.
Of course, no matter how many theories are, they are not as powerful as practical actions. For example, an internationally renowned sports brand has publicly stated that many of its best-selling running T-shirts are made of this kind of yarn. The reason is very simple because only in this way can it truly meet the growing functional demands of consumers and also allow the brand image to be obtained. Further consolidate and increase market share.
then when we decide to introduce such high-end materials, how should we judge which model is most suitable for the actual production situation of our own enterprises? Here are some suggestions for reference only:
first, define the characteristics of the target audience group and then determine the focus direction of the fabric;
second, comprehensively consider the budget scope to avoid waste of resources caused by blind comparison;
third, actively seek professional teams to help evaluate whether the existing technical level can smoothly connect with the development tasks of new models.
Looking to the future, with the continuous progress of science and technology, I believe that more innovative achievements will be applied to the traditional manufacturing industry to promote the development of the whole industry to a new level. Especially in the current environment where the concept of green environmental protection is deeply rooted in the hearts of the people, how to balance the relationship between economic benefits and social responsibility will become an important topic that all practitioners must face, which is worthy of in-depth discussion and research.
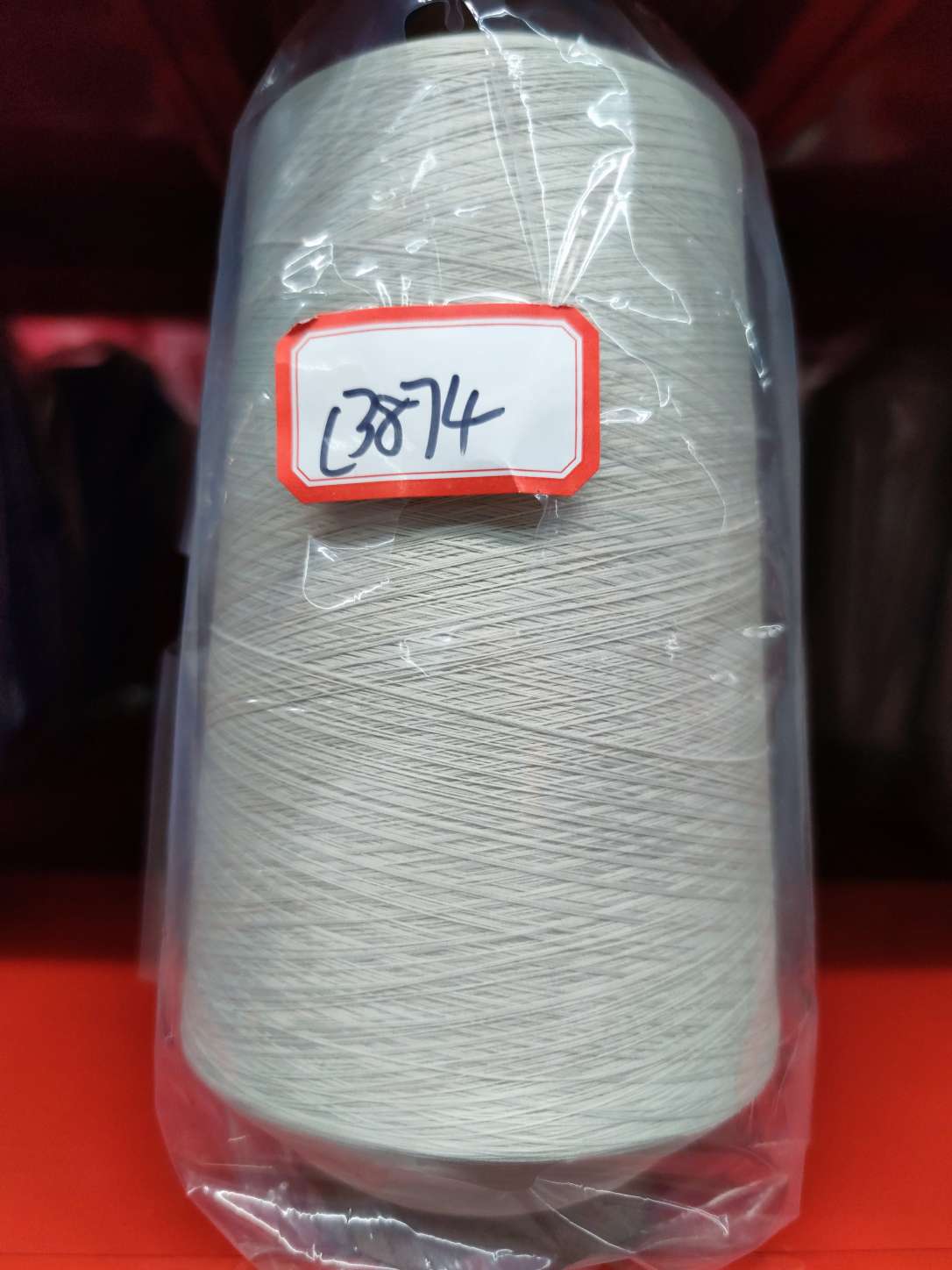