
In the textile industry, nylon high elastic yarn has gradually become the first choice for many brands and consumers due to its unique characteristics and wide range of applications. Today we will learn more about the story behind this magical material.
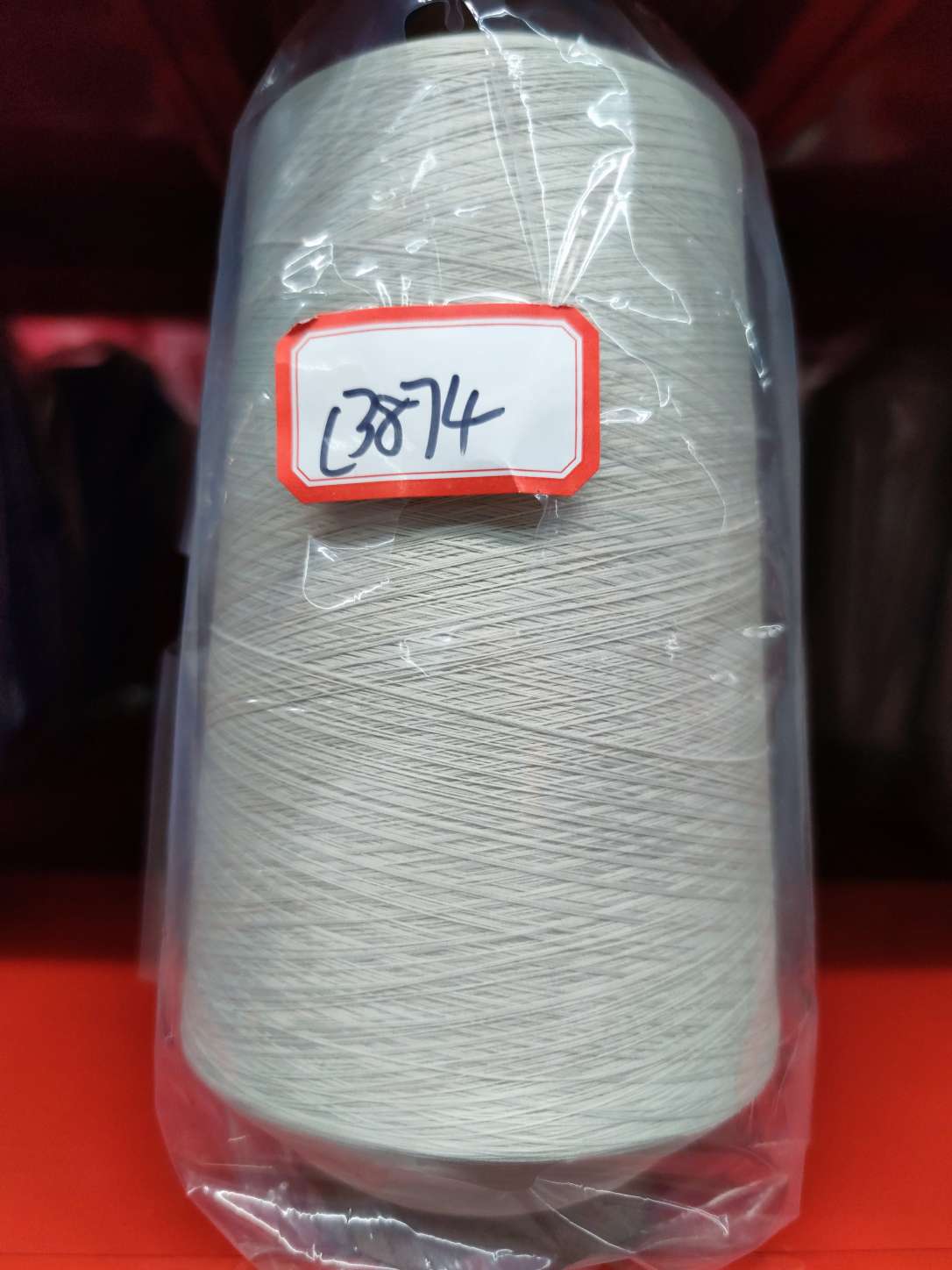
Material exploration: revealing the core composition of nylon high elastic yarn
Nylon high elastic yarn is a composite yarn composed of high quality nylon fiber and spandex through advanced coating process. Among them, 70D and 140D represent different fineness specifications, which are suitable for the manufacture of light and thin fabrics and thicker products. The yarns of these two specifications have excellent elastic recovery ability and excellent hand feeling performance, which can well meet the diversified needs.
Feature analysis: Why 70D and 140D spandex covered yarn?
Compared with traditional single-component yarns, nylon high-elastic yarns have more prominent functional characteristics. The first is its super elasticity, which can quickly return to its original state after stretching and is not easy to deform; the second is excellent abrasion resistance, which can still maintain the original luster and softness even after repeated washing; finally, it has good air permeability and moisture absorption and perspiration effect, which is especially suitable as one of the main raw materials for sportswear or other functional clothing.
Quality Choice: How Nylon High Elastic Yarn Meets Various Scenarios
whether it is the pursuit of comfortable experience of daily household fabrics, or the need for high flexibility of professional outdoor equipment, or even high-end fashion areas of customized services, you can see the figure of nylon high elastic yarn. It can adjust the corresponding parameter settings according to the specific purpose, so as to achieve the best matching effect. For example, when making tight pants, a high-density organizational structure is used to enhance the supporting force; while in the production of summer dress, it tends to choose a more sparse design scheme in order to achieve the purpose of cool and refreshing.
Process innovation: analysis of the whole process from production to finished product application
the birth of nylon high elastic yarn can not be separated from a series of sophisticated processing processes. The first is to strictly control the quality standards from the raw material procurement link, and then enter the spinning stage to use the latest technical means to ensure that each small unit can be evenly distributed and closely connected. The next step is to go through the dyeing and finishing process to give color diversity while further consolidating the physical and mechanical performance index value. The final delivery to downstream customers also need to complete a full range of testing and certification procedures to confirm that it is correct before it is allowed to be put on the market for circulation and sale.
Market Insight: Development Prospect of Nylon High Elastic Yarn in Future Trends
With the continuous improvement of consumers' awareness of health and environmental protection and the acceleration of new material research and development driven by technological progress, it is expected that in the next few years, the global demand for such high-performance synthetic fiber products will continue to grow. Especially in the context of the rise of smart wearable devices, a new model version with good mechanical properties and compatible with the embedded design requirements of electronic components may soon come out and lead the trend.
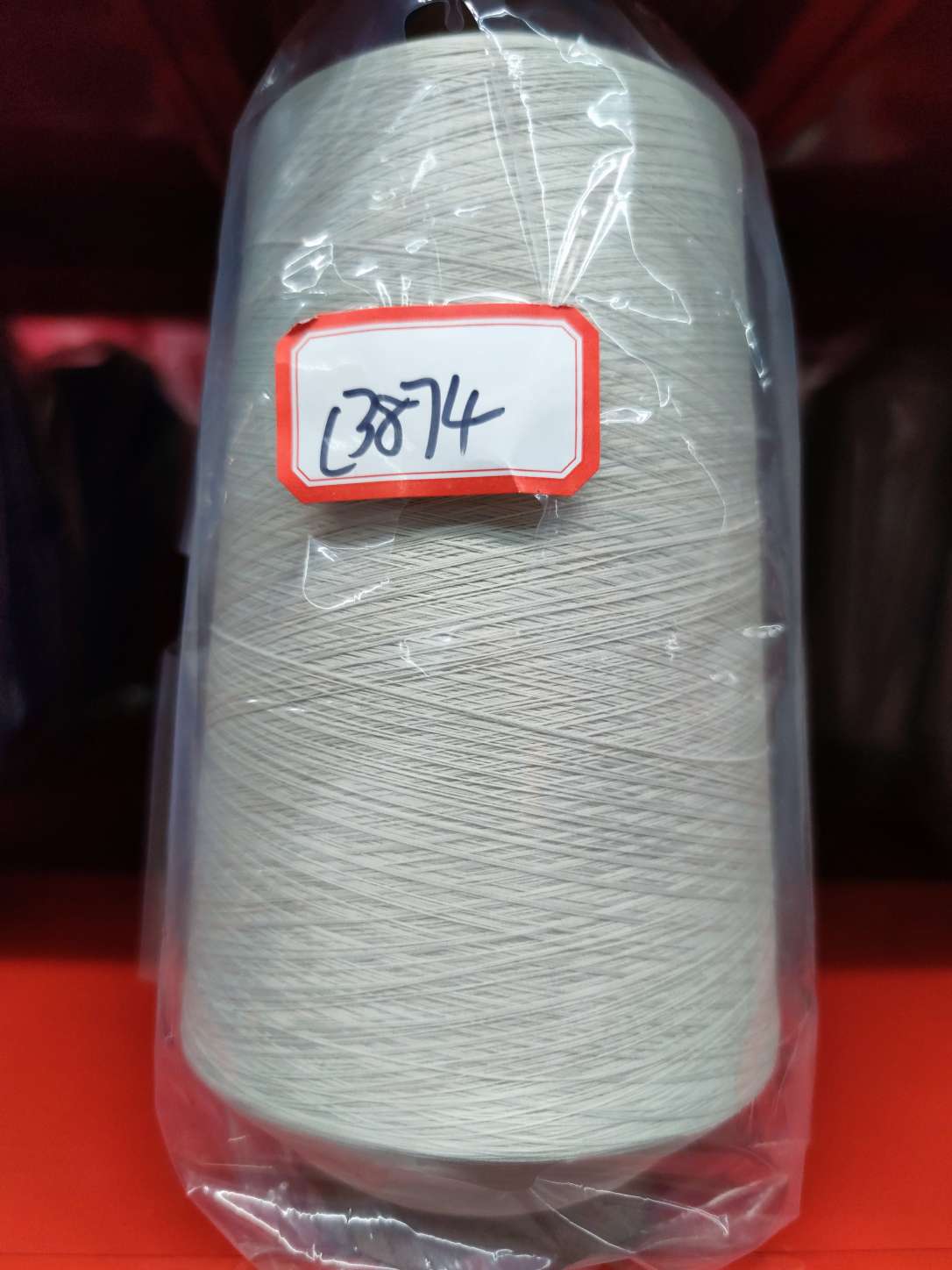